About Us
Mazenet Solution, in its 23+ years of multifaceted existence has constantly upgraded and invested in engineering, human resources, technology and equipment. The multi-vertical service provider remains a step ahead of tomorrow’s needs, positioning itself to meet the future of the entrepreneurial world.
An exclusive attendance management system AIMS, keeps track of, records information about employee attendance in the workplace. It assists in tracking the real-time production status, allocates job sheets, employee attendance reports which enables to reward the employees with incentives as per Chittaranjan Pattern Incentive Scheme. With discrete manufacturing process, planning the manufacturing schedules across various departments is made much easier.
Download pdf:
AIMS Product Brochure.pdf
Features

Oversee Production
The AIMS software tracks all manufacturing processes, right from demand registration to dispatch of finished products. This gives a complete view of the entire process and overview the developmental stages of each registered demand.

Allocate Job Sheets
The software aids in assigning job sheets for the employees, reads the employee working hours and calculates the time taken for completing each Job Sheet.

Effective Planning
With the track record of employee working status, AIMS software helps in effectively planning human resource operations and managing the materials required for the production.

Manage Attendance
The software is integrated with a biometric system that registers and records the entry and exit of all the employees, break times and records the exact working hours put in by every employee.

Award incentives
AIMS keeps track of employee attendance,the rate of productivity and completion of projects that helps in awarding incentives to the employees meeting the set deadline.

Quality Assurance
AIMS analyzes the quality of the product samples and overviews them for any issues or improvement. This ensures genuine planning with regard to sampling and inspection of the product thus resulting in an efficient product standard.
Overview
The AIMS software comprises five different sections with varying log-in access to
track the attendance and production processes.
-
1. Marketing
The marketing section is for registering work orders and Intend Registration received from consignees/controlling officers. Users with ‘marketing log-in access’ can enter the Master information for products, Units, Departments, Divisions, Controlling Officers, Consignees, Bill of Materials and Hourly Rates. It also records and maintains demand register, work order, MDS, supply-demand and consignee work order.
Features
- Prepare Bill of Materials
- Register Demand for products / Components
- Generate Work order based (SRR / Demand /
- Production Schedule)
- Prepare Production Schedule
- Allotment Advice
Reports
- Work order report
- Demand report
- Consignee work order report
-
2. Planning
The planning section is used to draw up production schedules based on the requirements generated from the marketing sector. Users with ‘planning log-in access’ can enter the products, trade groups, components & spares and rates. It also maintains and registers demand tender, Purchase order, production schedule, overall manpower calculation, production plan and procurement memo.
Features
- Manage Products, Components, Rates, Vendors, BOM
- Prepare Production Schedule
- Estimate Resources required
- Generate Procurement Memo
- Generate Purchase Order
Reports
- Schedule report
- Purchase order report
- Description Revision report
- Daily material receive report
- Coverage report
- Supply position report
- Stock position report
- 3. Rate Fixing
The production schedule generated from the planning section is used to assign job cards to the employees using the rate-fixing section. Users with ‘rate-fixing log-in access’ can enter the Master information for Shops and Operation. It also creates and maintains job cards, cancel job cards, and material requisition.
Features
- Manage Shops, Sub-assemblies and Operations
- Material Requisition based on the Work order
- Manage Job Cards
Reports
- Job card report
- Material Requisition report
- Work order position report
- Consolidated job card track report
- 4. Inspection
The inspection section is for storing the data collected from quality assurance tests. Users with ‘inspection log-in access’ can enter the Test type and manage sampling plans, inspection plans and component levels and view purchase orders. It also documents and maintains IDN register, result IDN, close IDN, material requisition and condonation form.
Features
- Manage Sampling Plans, Inspection Plan and Component Levels
- View Purchase Order
- Register IDN
Reports
- IDN report
- Component report
- 5. Progress
The progress section enables in generating the delivery challan . Authorized users can generate DC(Delivery Challan) whenever any product is dispatched from the workshop.
Features
- DC (Delivery Challan)
Reports
- DC Report
- JC Report
- Overall WO Report
- Consolidated JC Track Report
- 6. Workspace
The Shops section brings together the process details from the previous sections and manages job allocation based on employee attendance. This section manages Employees, Attendance and Shifts, and allocates Job Cards.
Features
- Manage Employees and Shifts
- Material Delivery Sheet, Delivery Challan, Attendance
- Job Card - Allocate, Check-In, Check out
Reports
- Attendance report
- Job card report
- Delivery challan report
- Gate Attendance report
- Incentive report
Application Screens
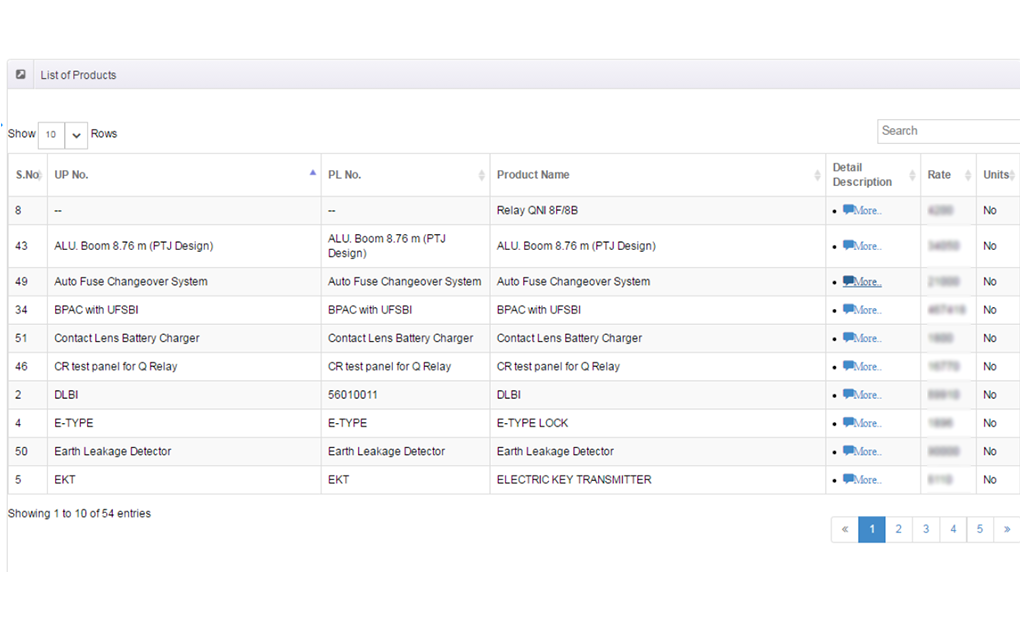
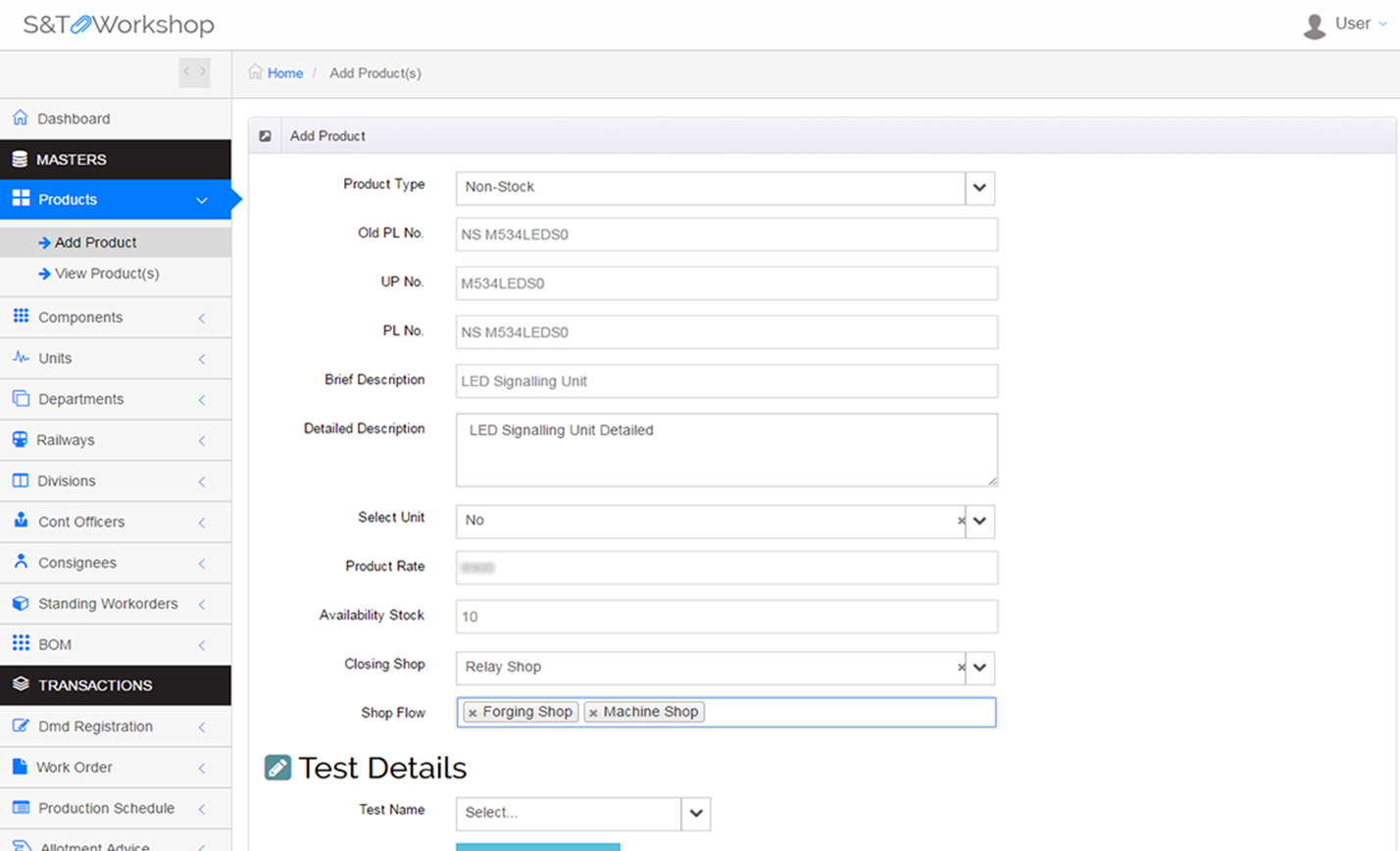
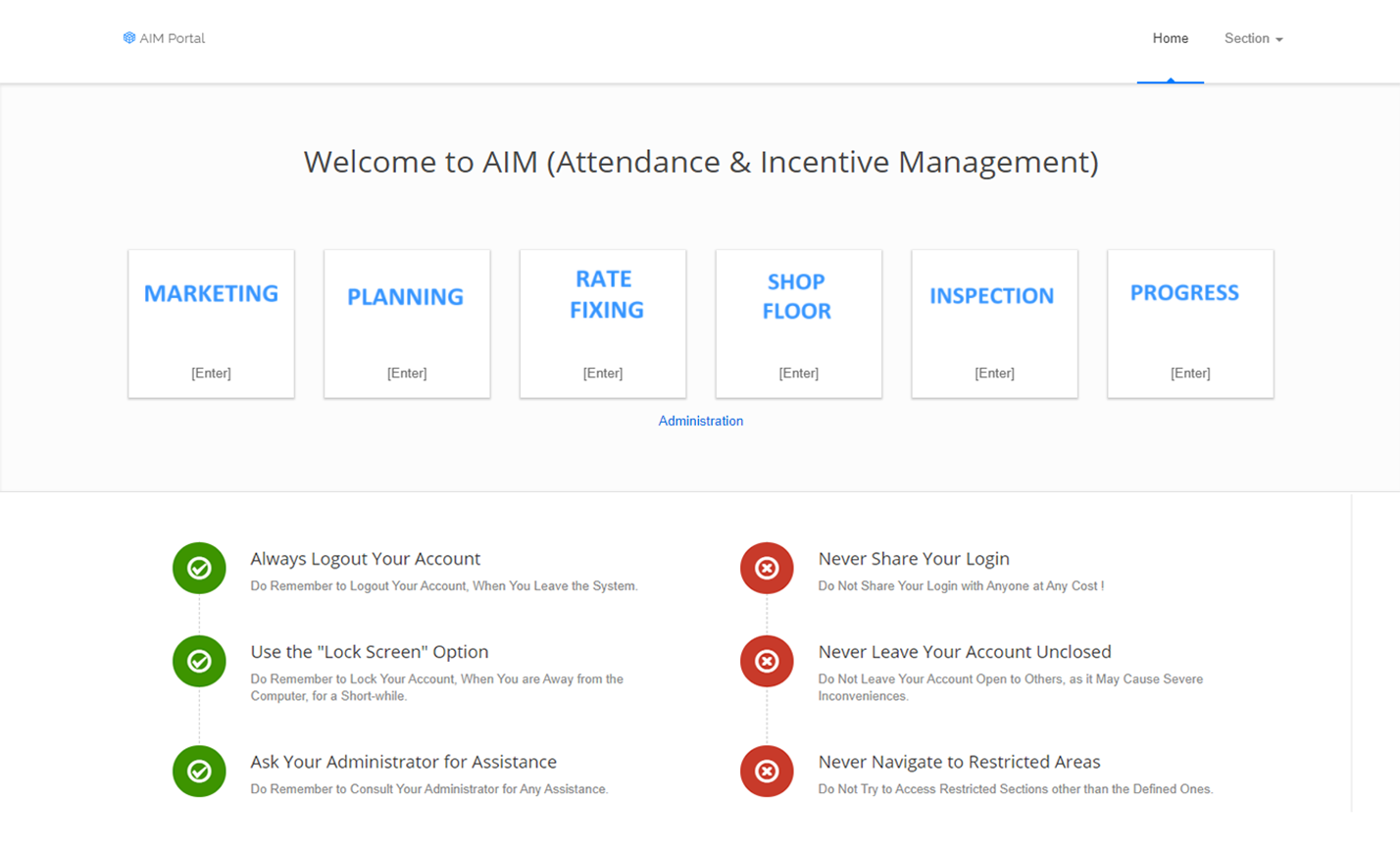
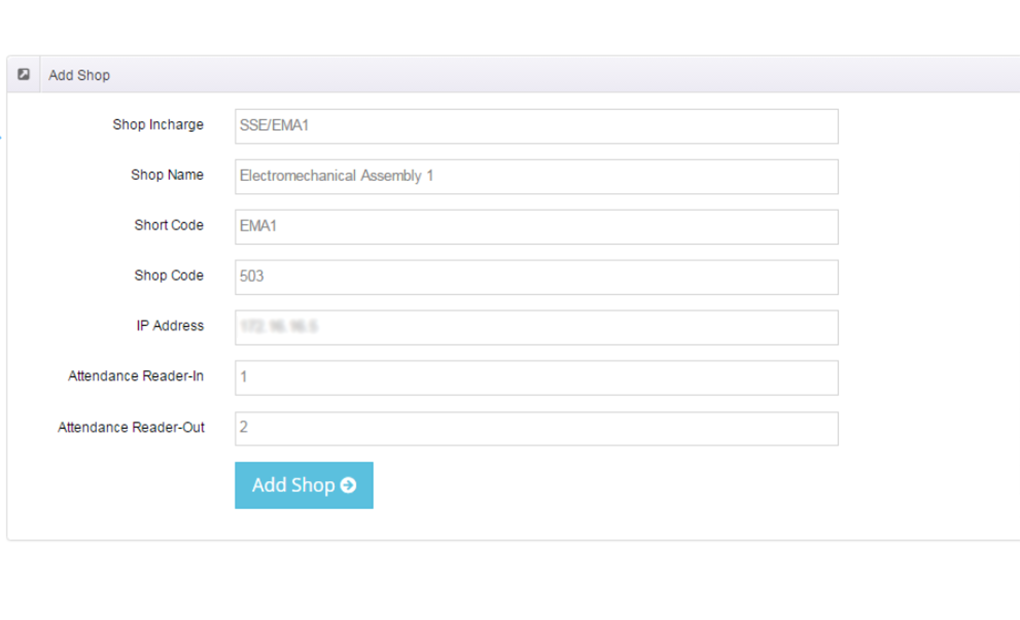
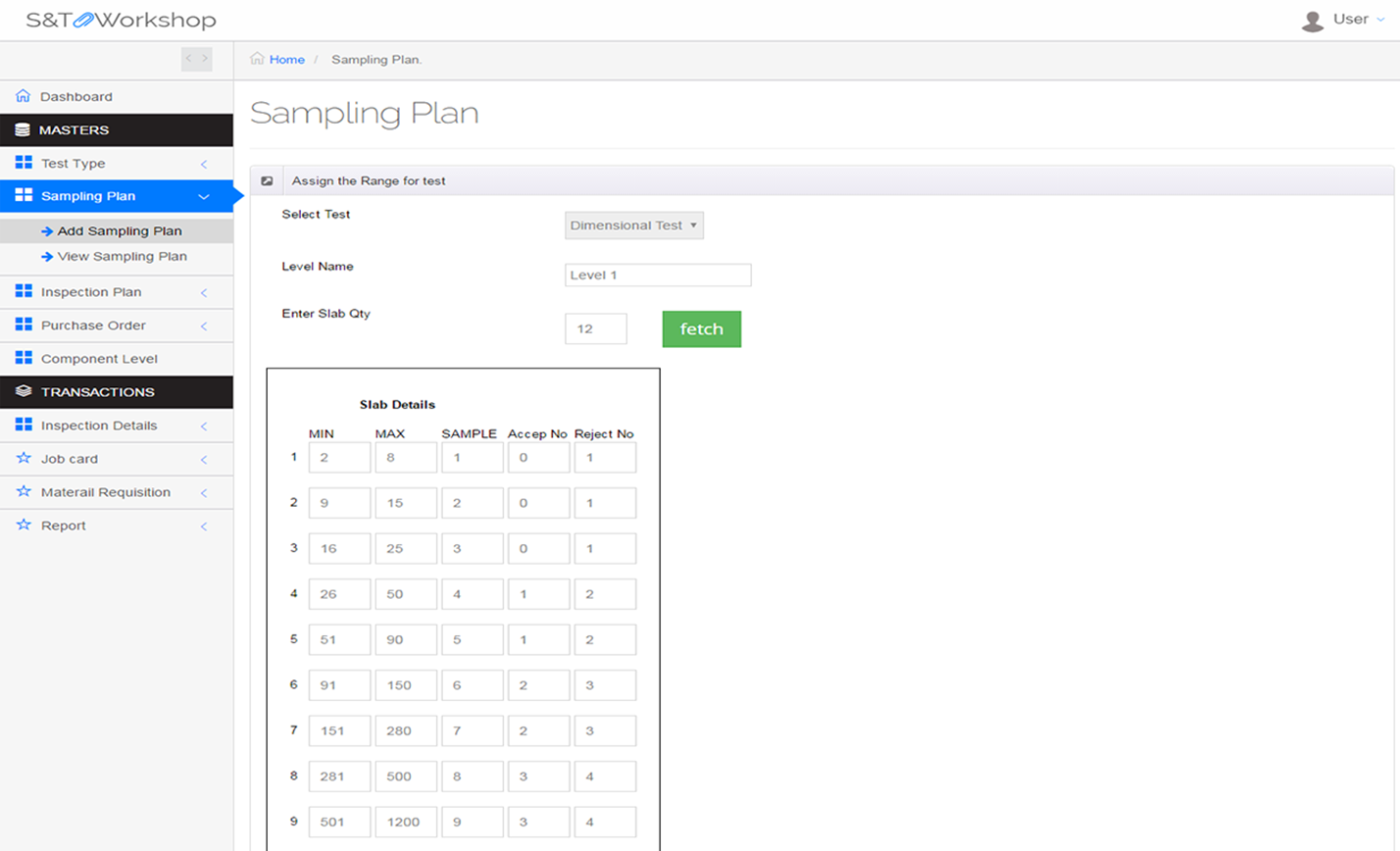
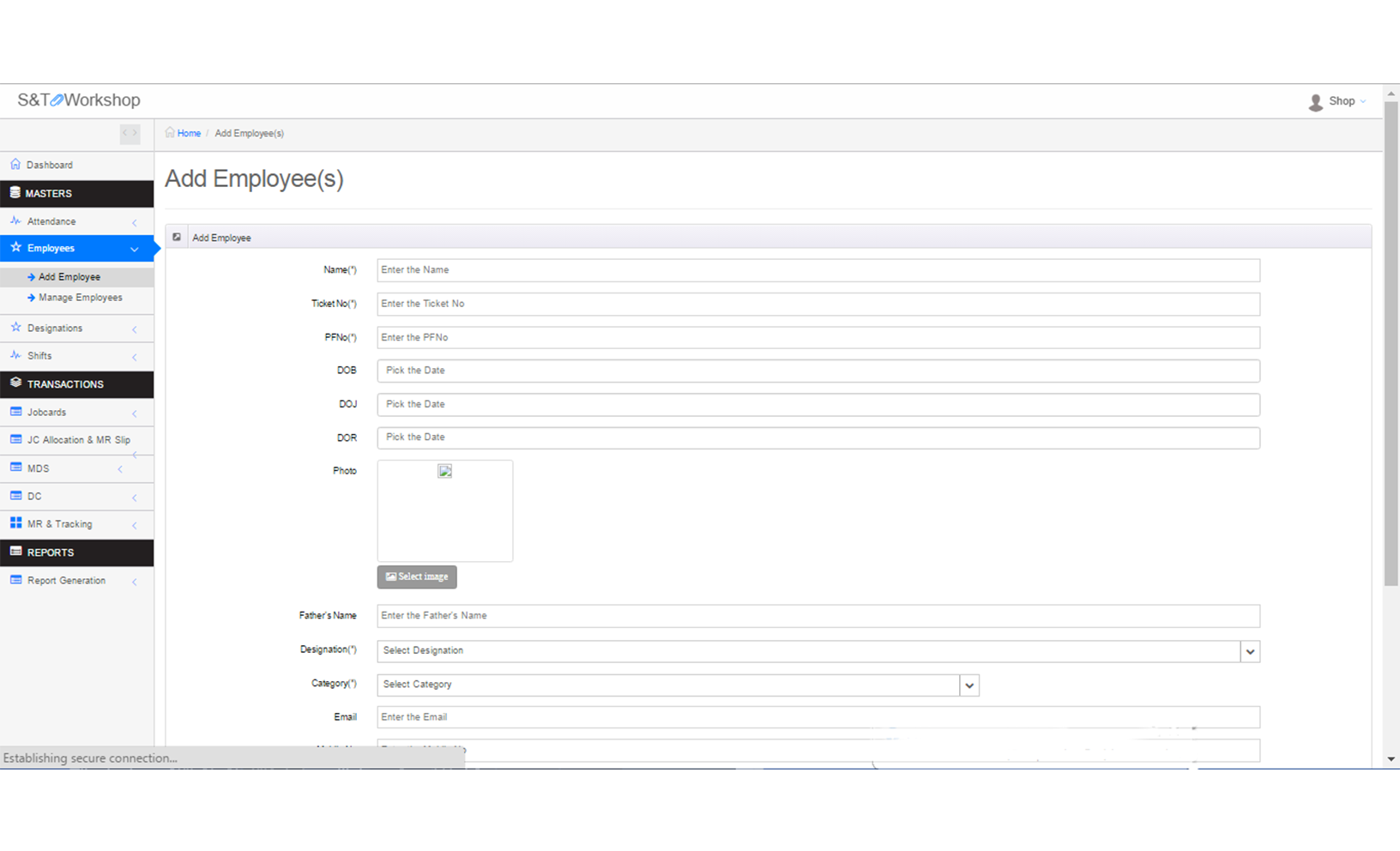
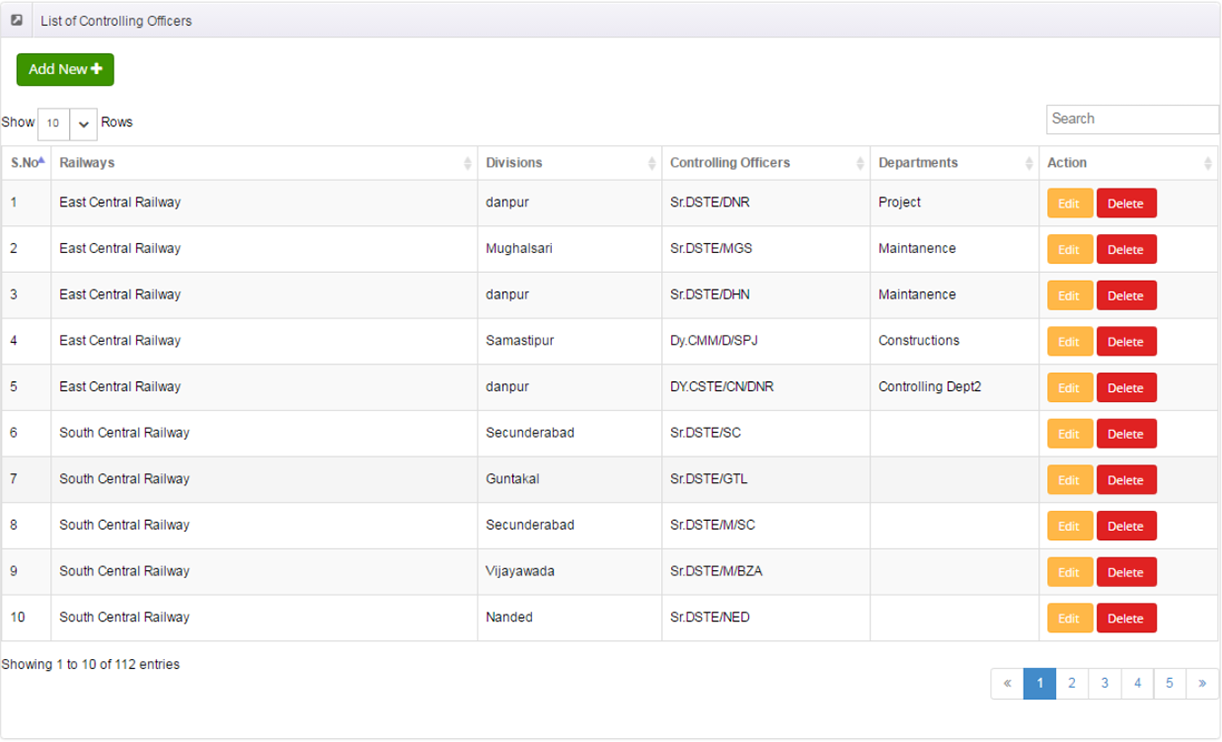
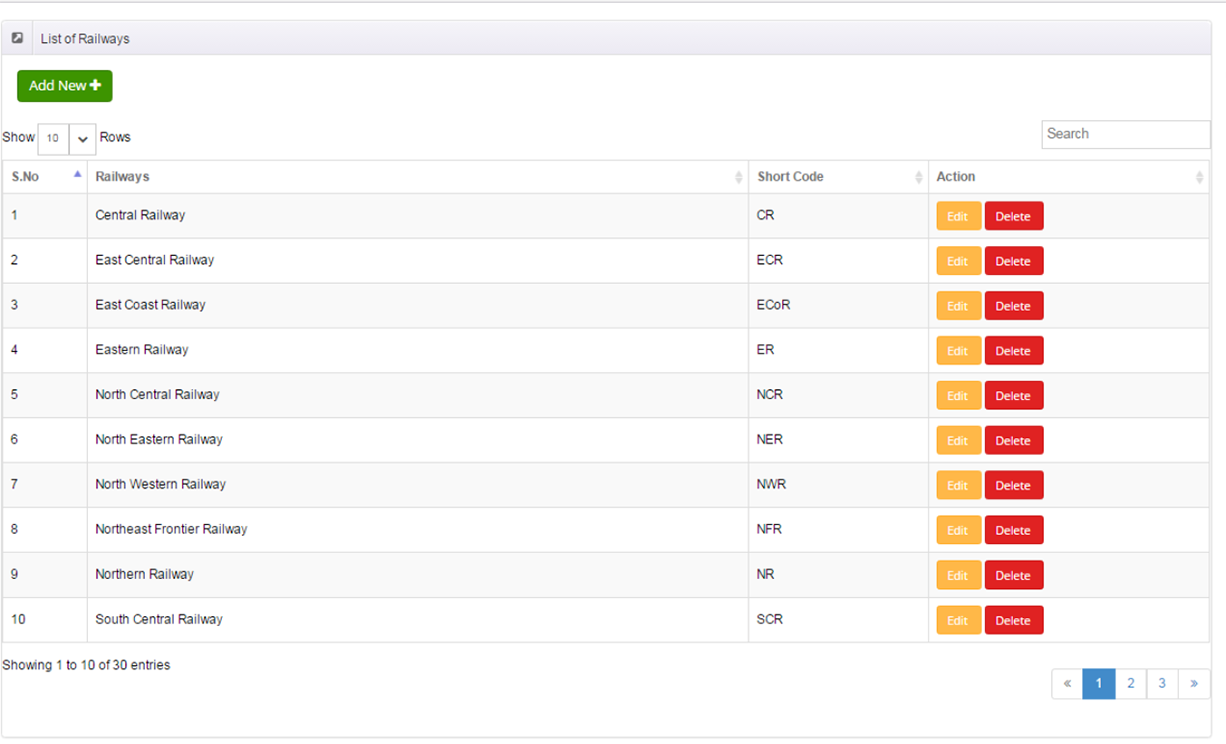
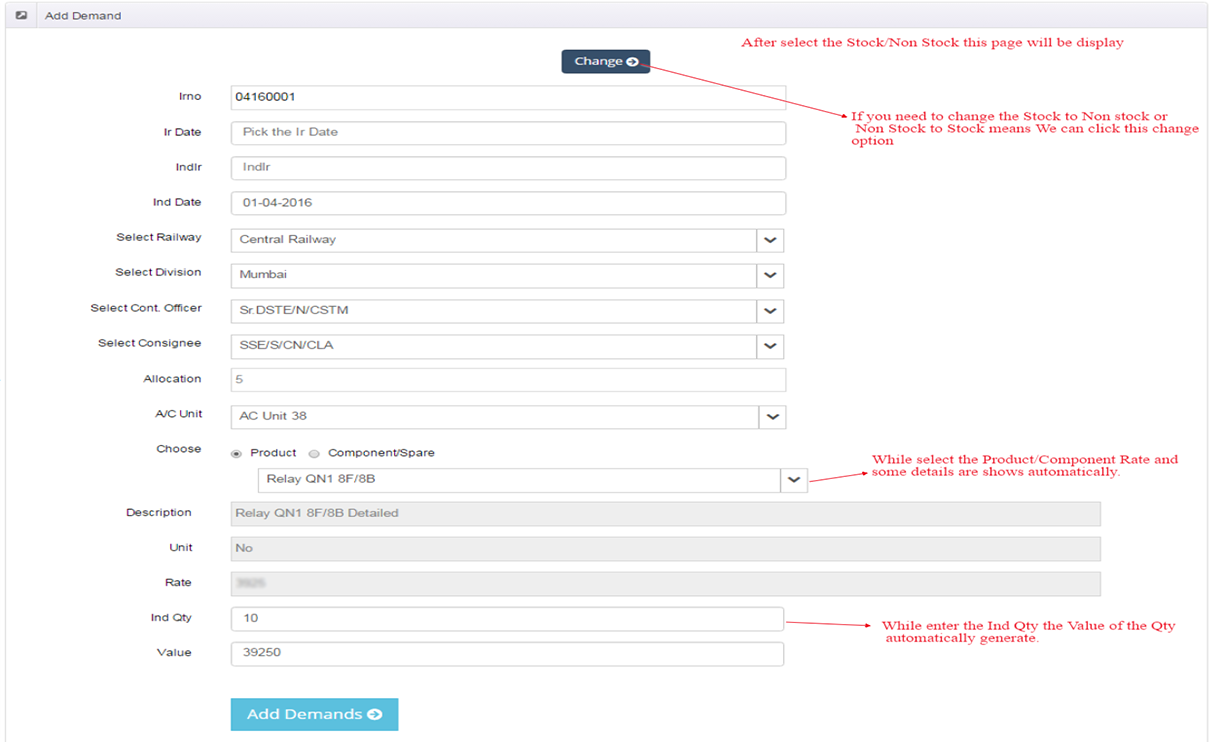
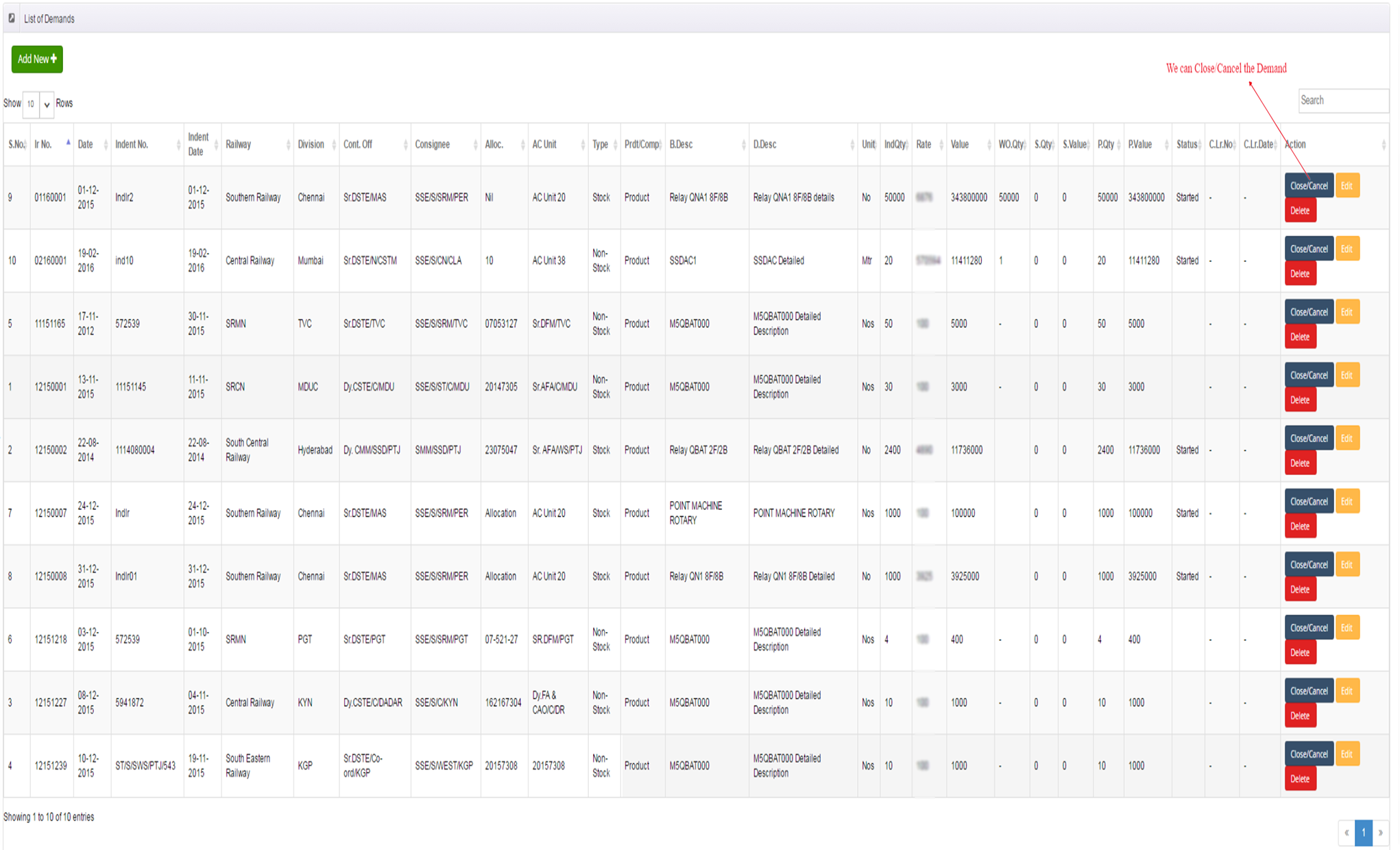
Reach Us
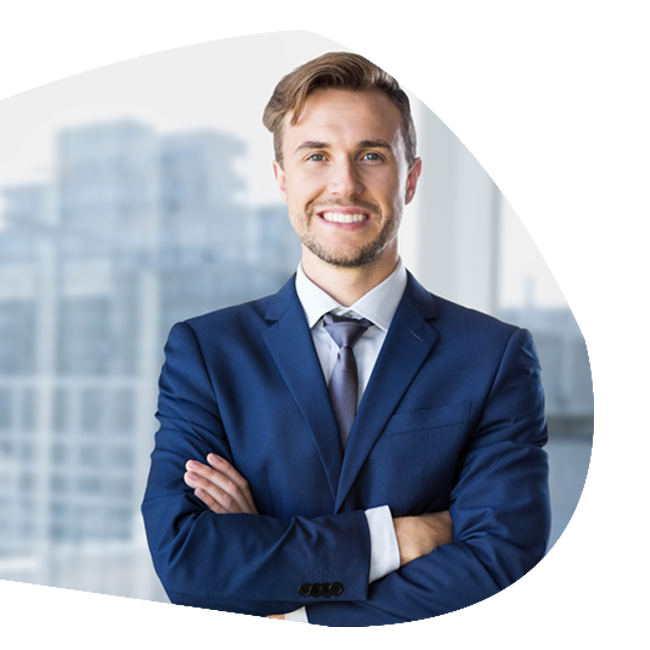